- keyword
- Volute Springs
- Compression Springs
- Rectangular Wire Helical Springs
- Conical Springs
- Disc Springs
- Flat Springs
- Extension Springs
- Torsion Springs
- Friction Springs
- Flat Spiral Springs
- other type of springs
- Calculation
- stainless steel
- spring rate
- piano wire
- leaf spring
- compression spring
- stress
- service life
- i-mc
- spring selection
Question Tokai Springs 2017/8/28(Mon) 11:09
About the “Spring selection”
A simple word “spring” denotes different objects with various shapes and a wide range of uses and
operations. What shape is most suitable for such use and such operation? What strength is required?
It is necessary to consider many factors one-by-one when designing a spring.
If you need a spring, do not hurry and wait a little before ordering a coil spring!
If a spring is not designed appropriately, without confirming and verifying specific usage environment and,
of course, required strength, it will rust or break in a moment.
In this text we will introduce the knowledge necessary for proper spring selection./p>
Since this text contain simple expressions to make understanding easier for all readers, please be sure to
contact us when actually designing or selecting a spring.
Contents
1. Spring definition and functions
・1-2-1 Fixed relationship between load and deformation
・1-2-2 Accumulation of elastic energy
・1-2-3 Natural vibration frequency
2. Types and characteristics of springs
・2-1 Classification of springs by material
・2-2 Classification of springs by shape
1.Spring definition and functions – Is the word “spring”
derived from “spring up”?
Although the word “spring” is often used casually, this word has a long history. There are different opinions
about its etymology, but the prominent theory is that this word is derived from the word “spring up”.
In English the word “spring” also contains the meaning of “spring up” or “leaping”, and indeed,
such movement is often associated with spring operation.
1-1. Spring definition
It is difficult to imagine a real object when hearing the definition of a spring.
The Japanese Industrial Standard defines spring as a “machine element whose main purpose is to utilize the energy accumulated by elasticity or deformation of a material body”(spring terms in JIS B0103).
Putting simply, spring is an element that has the ability to deform under applied force and then use this force to return to its original shape. Conversely, any object that can return to its original shape after being
deformed by applied force, can be considered a spring.
Thus, why do substances have restoring force to return to original shape after deformation?
Two different forces act on atoms that make up a substance: attracting force, trying to pull them to each
other, and a repulsing force that tries to separate them. Normally these two forces are balanced, keeping
a certain distance between atoms. When an external pushing force is applied in this balanced condition,
atoms and molecules are forcibly pushed closer together, increasing the repulsive force. It is the same image, as with a rubber, which has stronger resistance the more it is squeezed.
When the external pushing force disappears, the substance returns to its original state similar to separating magnets.
Conversely, when a pulling force is applied, the substance stretches, increasing the attracting force between molecules. Likewise, when the pulling force disappears, the material shrinks, returning to its original state,
like rubber returns to original shape.
Springs likewise have the restoring force. However, this deformation was measured mathematically only
recently, in the second half of 17th century. British physicist Robert Hooke discovered a linear relationship
between force and material deformation that was named Hooke’s Law. And the constant of the proportional relationship in the Hooke’s Law is the spring constant.
1-2. Spring functions
The restoring force of a spring was mentioned in the spring definition, but in reality there are five “abilities”
or “functions” of spring related to this restoring force.
1-2-1. Fixed relationship between load and deformation
As stated by the Hooke’s Law mentioned earlier, there is a fixed relationship between force (load) and
deformation. Depending on spring type, it may not always be a uniformly beautiful straight line, but there is
always a certain relationship between force and deformation in any spring.
1-2-2. Accumulation of elastic energy
When a force is applied to a spring, the spring is in a state of accumulating energy. This energy is called
elastic energy, which is converted into kinetic energy.
When the force applied to the spring is gradually removed, the accumulated elastic energy is also removed. When the force is removed completely, the elastic energy also becomes zero.
1-2-3. Natural vibration frequency
When force applied to a spring is suddenly removed, the spring vibrates. This vibration depends on
“mass of the spring” and “spring constant” and has characteristic (natural) frequency
See calculation of natural frequency here.
The vibration may have significant effect in actual use of springs, such as in buildings and structures.
Therefore, when designing a spring, not only the spring constant
but also the natural frequency of the spring must be reliable calculated.
1-2-4. Vibration absorption
Contrary to what was said above, there is a function that uses the vibration frequency.
Vibration exists not only in springs, but also in machines and other objects.
Vibration of large machines may adversely affect buildings and other devices.
To prevent transmission of such machine vibration, springs are installed on the machines,
absorbing the vibration and reducing the effect on buildings and other machinery.
1-2-5. Impact absorption
Similarly to the vibration absorption, springs can be used to absorb impacts. As undoubtedly often seen in
everyday life, springs ere very effective in absorbing impacts, and are used for this purpose everywhere.
2. Types and characteristics of
springs
– there are many classifications!
When speaking about springs, we usually imagine a coiled round spring. However, there are many kinds of
spring used in industrial word, and they can be classified in different ways.
2-1. Classification of springs by material
While springs are generally made from metal, springs from other materials, such as ceramics and carbon
fibers, are also gaining popularity recently.
The main advantage of non-metallic springs is their lightness.
In addition, air springs containing gas like a balloon are widely known as springs used in suspension
of trains due to low spring constants and simplicity of the mounting height adjustment.
Table. Classification of springs by material
2-2. Classification of springs by shape
Next, we will explain the classification of springs by shape. Like the classification by material, springs can be
classified by shape in many ways!
Coil springs
The majority of springs in the world are represented by coil springs. The shape of the springs is simple and
suitable for mass-production.
The coil springs can be further divided into 3 types: compression coil springs, tension coil springs
and torsion coil springs.
These springs are used in objects which are subjected to pressing force (compression load) applied from
above. While generally there are many round coil springs with a nice cylindrical shape,
there are also conical coil springs, barrel-shaped coil springs, springs wound with uneven coil pitch
and so on. In normal cylindrical springs there is a proportional relationship between load and
deflection with the spring constant as the proportionality constant. However, when the shape changes,
the relationship loses its linearity and becomes non-linear. There are many applications utilizing
this non-linear characteristic.
Unlike to compression coil springs, tension coil springs are used in applications where a pulling force
(tensile load) is applied. Hooks are often mounted on both ends of the spring to facilitate pulling.
The hooks themselves do not act as springs, but since a pulling force is applied, the strength of the
hooks must also be considered during design.
As with compression springs, there is a proportional relationship between load and deflection
with spring constant used as the proportionality constant.
The main difference of torsion coil springs from compression and tension coil springs is their usage;
the torsion coil springs are used where rotational motion occurs. The operation of torsion coil springs
can be understood by looking at clothes-pin and safety pin.
Unlike
compression coil springs and tension coil springs, torsion coil springs often have arms whose shape is
determined by the product to which the torsion coil spring is attached.
Disc springs
The disc spring is a cone-shaped spring with a hole drilled in the center of the spring like 5 yen coin.
The name (disc spring) of the spring is derived from its shape.
(Large size disc springs can be cut from metal parts.) Comparing to coil springs, the disc springs
can bear a very large load in a small space and, depending on design methods, can be designed with
non-linear load characteristic.
Leaf springs
Leaf (plate) springs are the springs with the largest number of shapes in the world. This is because almost
any used plate material acts like a leaf spring.
All plates that act like a spring, even bent ones and plates with holes, can be considered springs.
Disc springs made as plates can also be viewed as a kind of leaf spring.
Torsion bars
As the name suggests, the torsion bar is a rod. A spring rod with spring properties tries to return to original
shape when wrung. This force is used in torsion bars.
The elastic energy stored per unit volume is large compared to other springs,
so even light bars exert significant force.
There are stabilizers with arms attached to torsion bars which are used to stabilize cars.
Spiral springs
Spiral springs, also known as power springs, are springs using a force that tries to unwind a wound long thin
strip. A widely known toy ChoroQ uses this force to move forward.
The force of power springs is also used to pull back cord of vacuum cleaners with one switch.
These springs can accumulate large energy in limited space.
Spring washers, retaining rings
A spring washer placed between nut and bolt, in addition to the role of a washer, also serves as a stopper
between the nut and the object to be tightened. Bolts and nuts are less likely to become loose
when a spring washer is placed between them.
A wave washer looks like a normal washer with bulges and dents. It is stronger than a normal washer
and do not scratch objects it contacts. There are also wave washers made like compression coil springs,
called coiled wave springs.
As the name suggests, the retaining rings are springs used to fasten objects.
These springs are frequently used in the industry to fasten the parts that must be fixed.
All springs described above that are used simply to fasten some parts are called “fastener springs”.
Mesh springs
A mesh spring also known as a knit mesh spring, is made from thin spring material knitted like a cloth. This is a generic term for items used for cushioning. It has a belt shape in knitted state, but is made into cylinder
or donut shape when used.
Comparing to general cushioning material, the mesh spring has a higher ability to absorb vibration,
so it is often used in foundations for machines, engines and other devices prone to vibration.
Volute springs
Volute spring got its name from the similar looking shell-fish. The spring is made from wound long
rectangular stripe, similar to the spiral (power) spring, but unlike the spiral (power) spring,
it rises in a conical shape. When applied load increases (deflection becomes larger),
the spring constant gets stronger, which makes the spring ideal for absorbing large shocks.
Ring springs
The ring spring is a stacked up alternating combination of inner and outer rings with conical face.
When compressive load is applied to the ring spring, these two kinds of rings expand and contract,
exhibiting spring characteristics.
Since the frictional force is generated between two rings in addition to the expansion and contraction,
the design becomes considerably complicated.
There are also springs with non-fixed shape, like flat springs, wire springs, etc. A flat spring is a general thin
flat plate detail with spring action. A wire spring is a generic name for wires of various shapes with
round or irregular cross-section acting like a spring, excluding coil springs.
Thus, there are many types of springs divided by shape and material only.
It means that there is an appropriate spring for each application.
3. Designing a spring
Returning to the spring definition presented in section 1-1, we can say that in addition to restoring force,
springs also possess such functions as the fixed relationship between load and deformation,
the ability to store the elastic energy, the natural vibration frequency and the ability to dampen
vibrations and shocks!
It is natural that springs are used for purposes that lie among the spring functions listed above, but if a spring breaks after single use in actual usage conditions, it must be replaced each time.
Thus, the long continuous usage is the most desirable. The important thing is the lifespan of the spring.
3-1. Spring lifespan
The spring lifespan is the time period until spring breaks or loses its design characteristic as a spring.
The lifespan of a spring can be estimated to some extent by what kind of movement the spring performs,
its shape (degree of applied stress) and the environment the spring is operating in. For example,
a spring that maintains the fixed height almost without movement and a spring that stretches and
strings many thousand times will have completely different lifespans even with the same load applied.
Depending on shape, some springs may lose their characteristics with applied force on the order of
several tons, and some can support hundreds of tons. When used in special environment with high
temperature and humidity, springs of the same shape but made from different materials will have
different lifespans.
That is why it is necessary to design a spring.
3-2. Spring design methods
It is easy to determine the relationship between applied force and deflection and the lifespan of a spring to
some extent.
There is a wide range of free software, so please try it.
However, in practice the lifespan and load often do not act according to calculations, stressing the
importance of actual experience. If you have concerns about the design, please do not hesitate to contact us.
Answer Anonymous 2018/3/12(Mon) 15:51
Please tell me an easy way to divide a thin spring in the ballpoint pen in half.
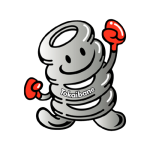
Answer Tokai Spring 2018/3/12(Mon) 17:04
Thank you for your inquiry, Spring Newbie! In the case of a normal coil spring, if you cut it in half, the end coil will be lost and therefore the spring can not stand or it will not be possible to compress the spring properly. It is not recommended to cut a spring in half because it will change the characteristics and accuracy of the spring. We recommend looking for a spring with a shape that you want. We are waiting for your custom-made spring requests! ! !
Answer 元禄箸くん 2018/3/19(Mon) 13:05
Hello. I was just wondering what the spring with the highest spring constant is to date and what its spring constant is. And by the way, what is your favorite food?
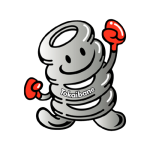
Answer Tokai Spring 2018/3/19(Mon) 13:21
Hello Genroku! Thank you for your inquiry! The spring with the highest spring constant?… This is such a difficult question. If the spring constant is large with linear characteristics, maybe it would be a torsion bar? The answer can be varied when considering the maximum spring constant, the material and shape, and the possibility of manufacturing… We can design a spring as you like if you can tell us the mounting method, space, required spring characteristics, etc. By the way, my favorite food can not be officially released, so…it’s a secret ♪ Thank you!
Answer Anonymous;コキ4号 2018/7/12(Thu) 13:48
1. When stating a tension coil spring, when it is desired to extend to a predetermined size with a force of 30 kg, can it be expressed as “a tension coil spring with a tension force of 30 kg …”? Is this unnecessary to state the spring constant?
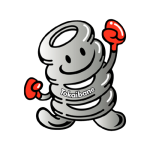
Answer Tokai Spring 2018/7/12(Thu) 14:01
Thank you for your inquiry, Koki 4 ⁇
A Spring Newbie! A tension coil spring with a tensile force of 30 kg cannot be specified as a specification, so I think it might be easier to understand by expressing it like this. (1) Tension coil spring that can obtain a tension force of 30 kg when stretched by 〇〇mm ② Tension coil spring with a spring constant 〇〇N / mm (Kg / mm) requires a maximum tension of 30kg or a maximum of 〇〇mm of deflection. When you state the spring like this, plus if you know the space to mount the spring, you can determine the shape accordingly. Once again, many thanks for your inquiry.
Answer Anonymous 2019/9/30(Mon) 15:48
Is there a way to stretch a spring nicely?
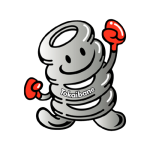
Answer Tokai Spring 2019/9/30(Mon) 15:58
Dear Spring Newbie,
“a way to stretch a spring nicely…?” You mean a tension spring, didn’t you? It is possible to stretch a tension spring nicely by aligning the radial centers of the fulcrums when the tensile force is applied. If the fulcrum shifts, the spring will extend in an oblique direction, so if the spring is a heavy spring, the coil may bend under its own weight. The effect is significant when a tensile load is applied in the horizontal direction. If “nicely” here means the spring’s shape, it may be improved by applying the suggestion above. If you are having trouble with the malfunction of the spring, please contact us here for technical support! Many thanks for your inquiry.
Answer Anonymous 2019/11/7(Thu) 13:13
How much of an equivalent force is applied when the maximum allowable load of a compression spring is 8N?
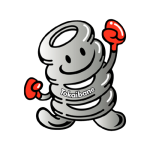
Answer Tokai Spring 2019/11/7(Thu) 13:51
Thank you for your inquiry.
1 kgf is the weight of an object with a mass of 1 kg under standard gravitational acceleration (g = 9.8 m/s2) (weight is the force when gravity is applied to the mass). Because mg is the weight of an object with a mass of m, the weight of a mass of 8 N equals to 8 N / 9.8 m/s2 = 0.82 kg
According to SSI Units and Unit Conversions: 1kgf = 9.8N; 1N = 0.102kgf
Answer Anonymous 2020/3/10(Tue) 16:06
To adjust the hydraulic pressure in a pistol, a compression spring (wire diameter 2Φ, diameter 30 mm, height 60 mm) is used in a compressed state at about 30 mm. When the oil pressure changes a little, will it still work effectively if I pull the spring and extend it a little? Will the strength of the spring returned? Will it become unusable if I pull it a little bit too much? Thank you.
Answer Tokai Spring 2020/3/10(Tue) 16:29
Many thanks you for your inquiry Spring Newbie!
When the form of a compression spring changes, it could be caused by the fatigue of the spring. In this case, you can temporarily fix it by pulling the spring back to its original shape. However, the same fatigue could possibly occur again in operation. If the hydraulic pressure is controlled, the fatigue of the spring will not occur even if the spring is compressed to the elastic limit.
If you can provide us the information regarding the structure and operating conditions of the hydraulic system here , we will be able to propose an optimal spring to you. Once again, thank you for your inquiry!
We are happy to answer any inquiries regarding technology, specifications, materials, etc. Please feel free to ask.