- keyword
- compression spring
Question 座巻 2006/10/13(Fri) 9:50
I’m studying the end turns of compression springs.
I often see that a total of two end coils at each end is common, but is there any difference if the springs moves with one end coil and two end coils (likelihood of entanglement of springs during compression, easy buckling…)? Please tell me in detail, thank you in advance!
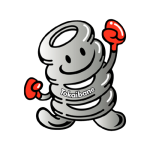
Answer Tokai Spring 2006/10/16(Mon) 10:03
Thank you for your inquiry!
Generally, each end of the spring has got 1 end coil.
The main purpose of increasing the number of end coils is to improve stability when the spring is mounted.
Each end has 1.5 to 2.0 coils to widen the polished part of the end surface (to the extent that the end thickness of the end coil part does not become too thin) and increase the flattened part of the spring to further improve stability!
Answer 座巻 2006/10/17(Tue) 11:35
Thank you for your answer!
I would like to confirm one more thing, when it is specifically said “when a spring is fixed, the stability is improved”, how does it stabilize?
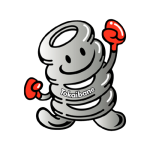
Answer Tokai Spring 2006/10/17(Tue) 14:50
Hello!
When the end coil is attached, the spring will be better seated and the load can be smoothly received when a compressive load is applied.
Thank you for you inquiry!
Answer Anonymous 2019/2/5(Tue) 11:49
Closed end (grinding) is a process in which the end part is coiled as a round material and finished only by grinding with a large grindstone. Closed end (taper) is a process of heating the part which is equivalent to 3/4 of the coil at both ends and rolling the round material with a taper roll machine to make it into a square cross section + a taper where the tip becomes thinner. It is more efficient than grinding from round material when finishing the end surface. It is mainly used for mass and medium production (vehicles, cars, construction machines, etc.). It is not suitable for small-volume production because it is necessary to set the taper roll individually.
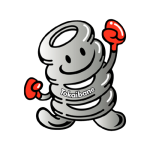
Answer Tokai Spring 2019/2/8(Fri) 17:08
Closed end (grinding) is a process in which the end part is coiled as a round material and finished only by grinding with a large grindstone. Closed end (taper) is a process of heating the part which is equivalent to 3/4 of the coil at both ends and rolling the round material with a taper roll machine to make it into a square cross section + a taper where the tip becomes thinner. It is more efficient than grinding from round material when finishing the end surface. It is mainly used for mass and medium production (vehicles, cars, construction machines, etc.). It is not suitable for small-volume production because it is necessary to set the taper roll individually.
We are happy to answer any inquiries regarding technology, specifications, materials, etc. Please feel free to ask.