第1話
火花立ち上がる
数年前、眞鍋造機株式会社の西条工場に加わった新たな仲間たち
モノづくりのなかで一番、時間のかかる溶接を難なくこなしてくれる
そのメンバーとは、職人たちの間に入って器用に働くロボット
「ここは、お前に任せたよ」そんな会話が聞こえてきそうな
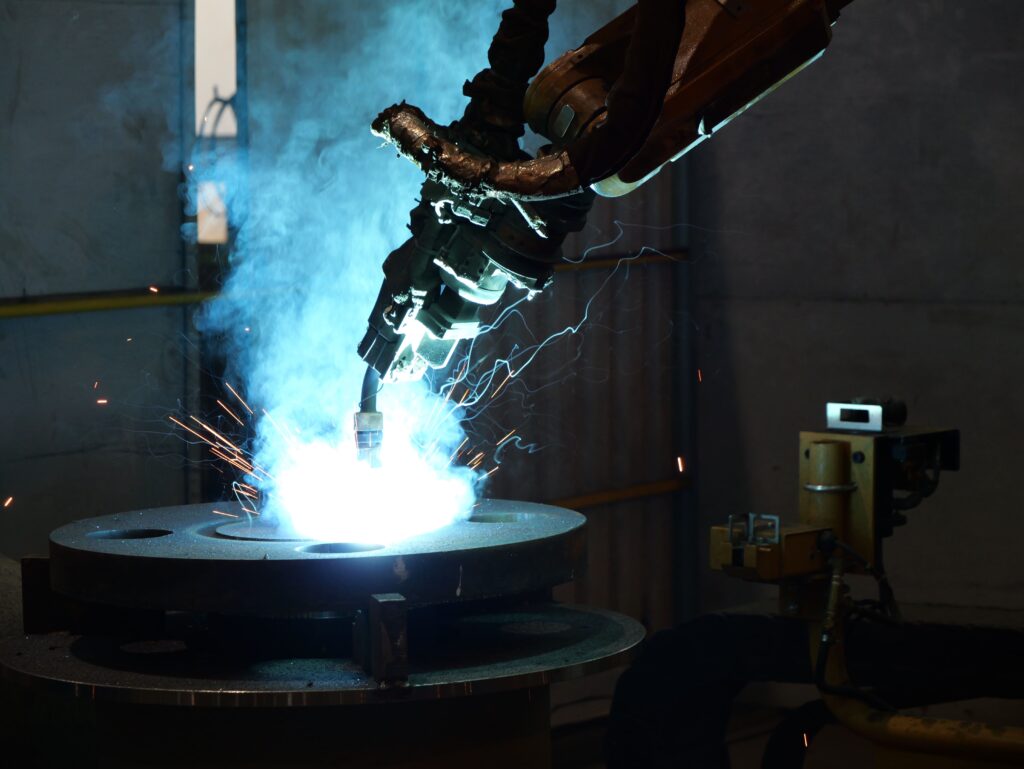
人と機械が共存し合う風景が、ここはある
海運業日本一と言われる愛媛県今治市は、機械メーカーや船舶運営会社がひしめき合う。2025年で会社設立65周年を迎える眞鍋造機株式会社も、船舶に搭載される機械のパイオニアとして海運業に尽くしてきた。その歴史を4代目となる眞鍋将之社長に、紐解いてもらった。
過酷な船の上
はじまりは、住友重機で働いていた新居浜出身の創業者が、再建王と称された有名な経営者から声をかけられたことからでした。今治に移り住み、鋳物屋をやりながら船舶に搭載する機械の製造をスタートさせました。鋳物はわずか5年で閉じ、船舶に搭載される甲板機械のウインチが主力製品となったのは1961年。その後、デッキクレーンが登場した80年代に、重工業メーカーのOEMとして製造したことから、ウインチとクレーンの2本柱で事業を展開してきました。
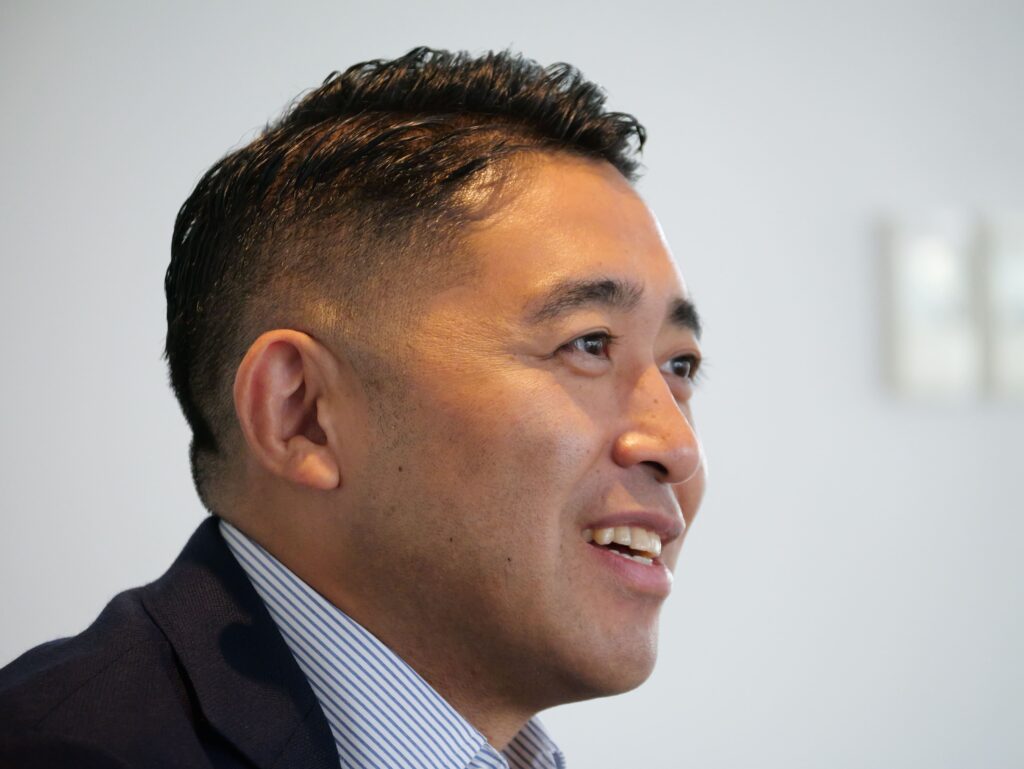
船舶用のウインチはドラムにロープを巻いていく機械装置で、船舶の係留や錨の巻上げ、巻き下げ作業に使用されます。常に荒波や潮風に晒される過酷な船の上で、激しい劣化に耐えながら20年、30年使用できる製品を提供しなければなりません。そのカギとなるのは独自の設計ノウハウですが、素材の選定や鉄板の厚み、強度計算など机の上だけでは100点満点とはなかなかいかず、出荷後の対応がお客様の信頼を得るうえで大きい要素になります。
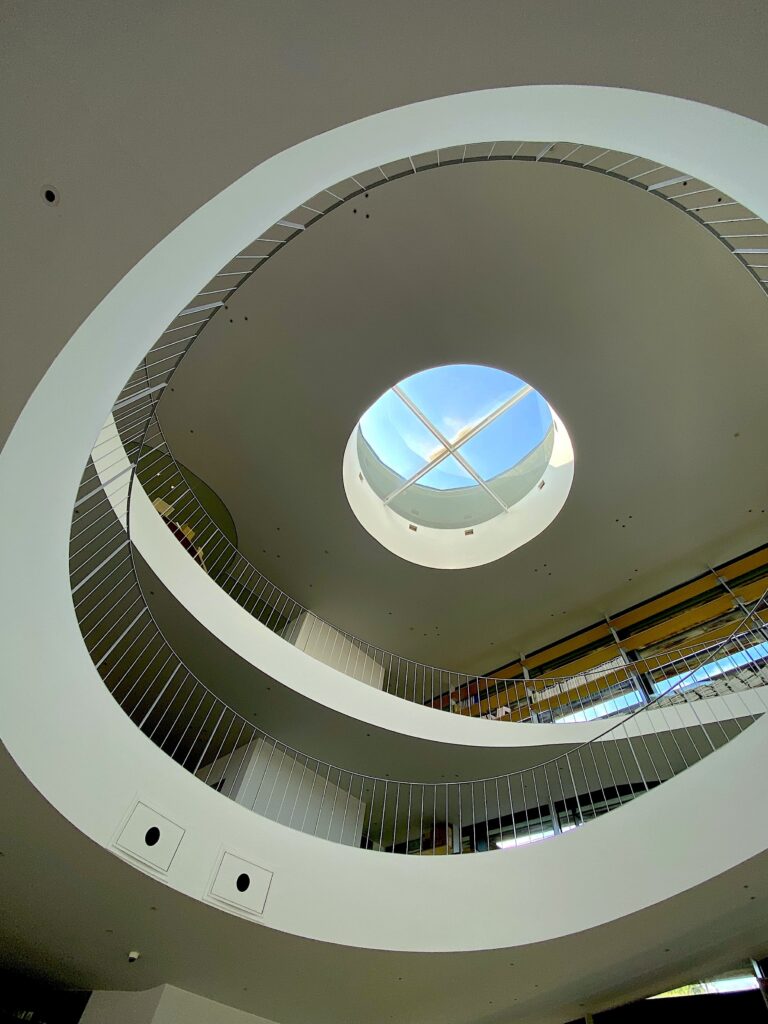
国内で使われる船を内航船、国外で使われる船は外航船と呼ばれるなかで、我々の主力は外航船。船の業界は少し複雑で、製品は造船所殿におさめますが、最終ユーザーは船主さん。いいものをつくるには船主さんのフィードバックが重要で、その関係性を築くことがとても大切です。
独創の風土
眞鍋造機(以下:眞鍋)の強みは、標準的な製品だけでなく、オーダーメイドな特殊品もつくっているところで、それを好んで手がけてきました。業界の歴史をみても、標準的な大量生産だけを行っている会社は淘汰され、差別化できる”何か”を持っているメーカーが生き残っています。我々が今日まで生き残ることができたのも、ブレずにモノづくりをやってきた結果だと思っていますが、その独創性は創業の頃から培ってきた風土です。他社がやりたがらないところで1歩先、1歩先を積み重ねてきました。
例えば、他社が鋳物を多用しているところを、眞鍋は鉄板などの素材から自社で製造しています。国内ではほとんど製造できなくなった鋳物は、中国からの輸入に頼らざるを得ないので、円安や物価の高騰でコストが合いません。素材からつくるということは手間はかかるものの、外注をせず改善に次ぐ改善でコストコントロールが可能となり、ここ数年の自動化で、さらにコスト競争力がついてきました。これが、生き残ってきた要因の一つだと考えています。
創業者が残した道しるべ
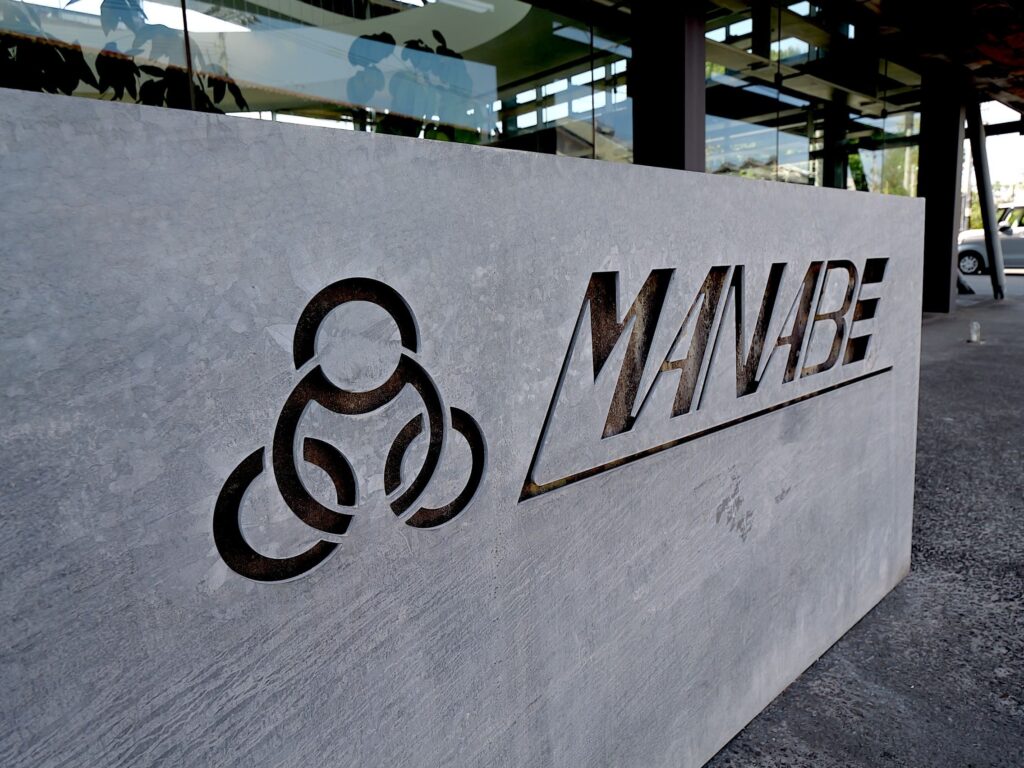
創業者が社是として掲げたのが、「独創・活力・研鑽」という3つの言葉で、これが道しるべになったと思います。そこへ、先代が経営理念を、私がビジョンとミッションを加えそれぞれの概念の役割を整理しました。ロゴマークは遊星ギアと呼ばれるもので、外の3つの丸が社是の3つを表し、中央の太陽ギアはよく見るとMなんです。眞鍋の周りに独創、活力、研鑽がかかっています。
事業継承の葛藤
そんな眞鍋で将来働くことを頭の片隅に置きながらも、大学時代から葛藤はありました。とにかく自分がやれることをやろうと、大学は経済学部を卒業してから工学部に編入し、経済と工学の学士を取りました。
ちょうどその頃、ITベンチャーが台頭しDeNAの南場さんとか、起業家が採用活動のために大学に来ては夢を語っていました。心底ワクワクしました。卒業後、一度はIT業界に就職したのですが、働けば働くほど悩みは深くなるばかり。答えを出せないのなら、眞鍋で働いてみようと飛び込みました

冬の時代
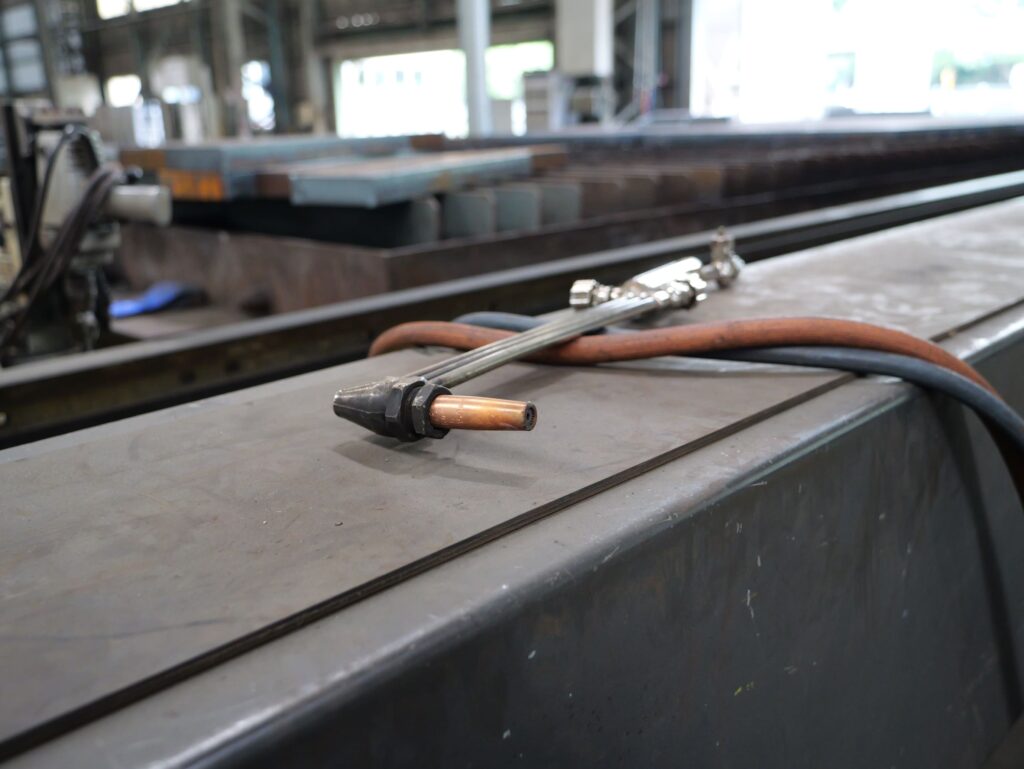
しかし、思うようにはいきませんでした。父から経営を引き継いだ時、業界は冬の時代に突入していました。需要が激減したところに、中国、韓国と競争相手が台頭し造船業全体が価格競争に巻き込まれてしまったのです。2014年以降、製品価格は下落し利益も圧迫され、そこから10年、本業で生き残れるかどうかの崖っぷちに立たされました。
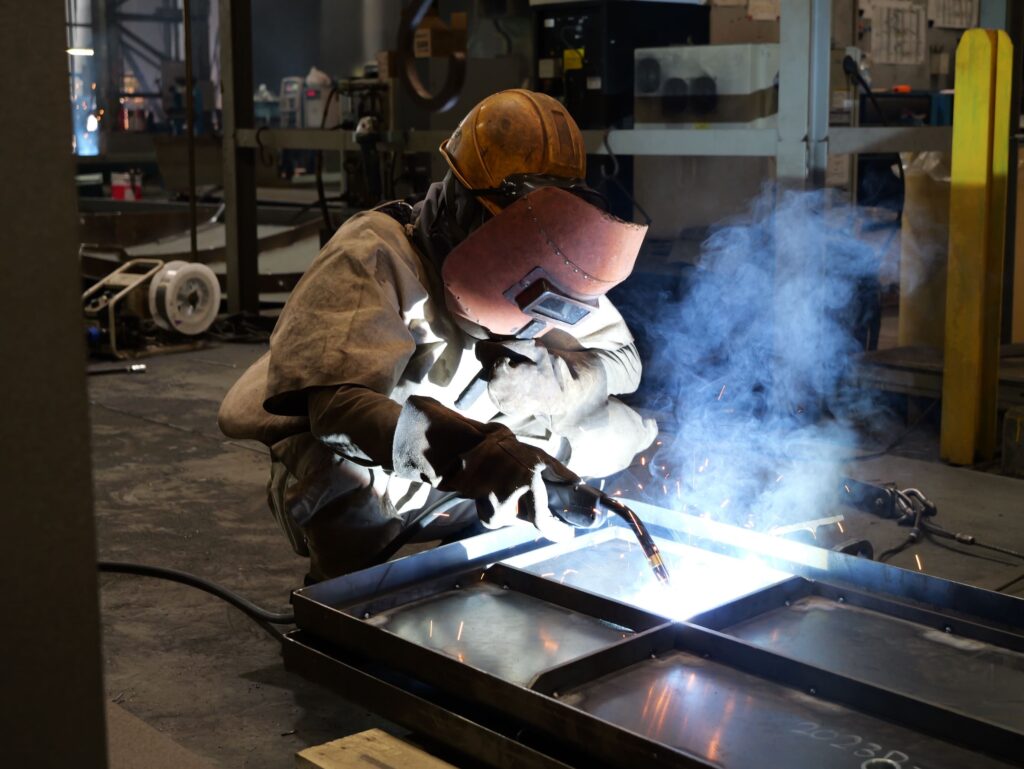
「先代の時代は良かった」という声も社内にはあったと思います。事業はボランティアではなく、儲けることでみんなに還元しなければなりません。外部環境の変化を言い訳にすることはできませんし、儲けを出さないことは従業員を裏切ることにもなります。苦渋の決断でしたが、それまで経験したことがない従業員の賞与カットも実施し、生きるか死ぬかの10年を過ごしました。
溶接の自動化
その中でやったことは、自動化の実現です。鉄と鉄をくっつける溶接の工数が膨大にあるため、まずは溶接の自動化に取りかかりました。早くからロボットは導入していましたが、その先へ進めていなかったのです。自動化に対する社内の”反対勢力”といったものはありませんでしたが、自分がやってきた作業がロボットにとって変わると感じていた社員もいたと思います。
溶接作業には、神経を使う難しい部分と神経を休めながらできる部分があるのですが、ロボット化はどちらかというと神経を休めながらできる部分に適しています。そこを自動化すると「自分たちの仕事は常に気を休めないじゃないですか」と言う人もいましたが、いざ自動化が進むとみんな楽になったのです。そこから「これも自動化しましょう」と声があがるようになり、工場は変わっていきました。
眞鍋では「どんどん楽をしよう」と言っています。楽とは、知恵を出すこと。付加価値を生み出すのは、知恵を出すか汗をかくかしかありません。汗をかくより知恵を出せるのならその方がいい。だから、楽をするために知恵を出そうと。知恵を出さずに楽するのは堕落です。この時代、人手不足は1番の課題ですから、自動化に大きく舵を切った効果は大きかったですね。働いてるみんなが、喜んでくれましたから。現在、西条工場で6台のロボットを導入、デッキクレーンの溶接箇所の約半分は自動化されていると思います。
視界が晴れて
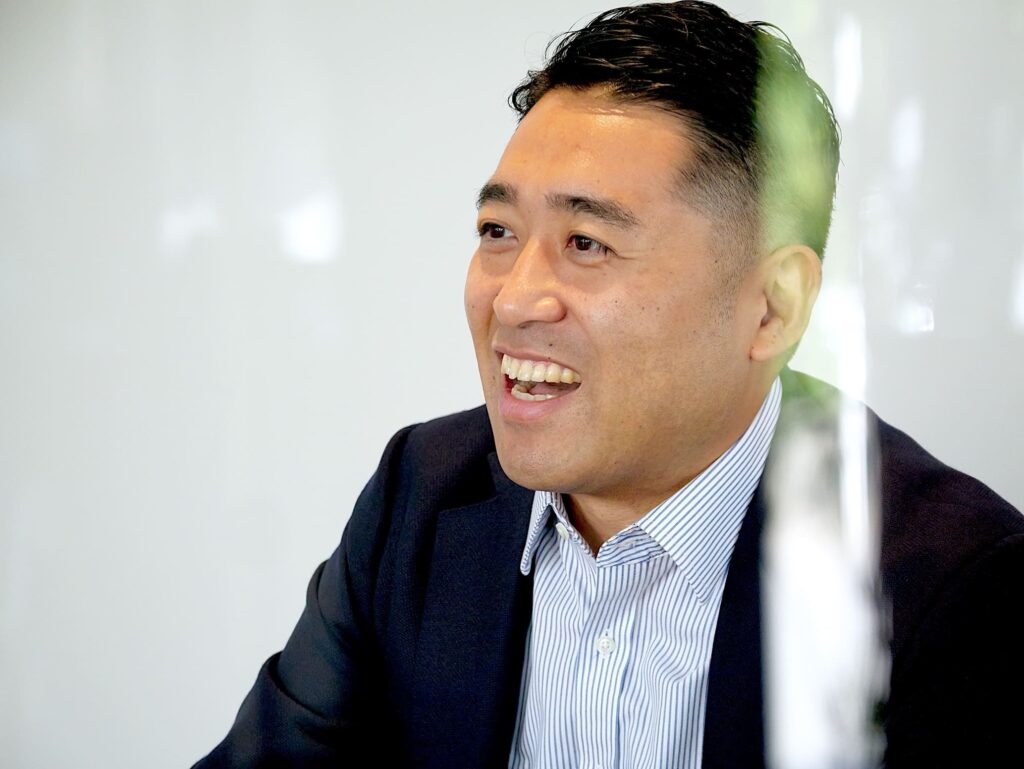
そうこうするうちに、業界の冬の時代が終わり、風向きが変わったのは2020年の春頃。国内に4社あったデッキクレーンメーカーも他社の撤退や統合により2社となっていました。業績が回復し利益を出せた時、2回カットした分を社員に返しました。眞鍋に飛び込み今に至りますが、30代はあっという間に過ぎ、気が付けばもう40代です。業界内では2029年まで仕事量が確保されていると言われているものの、未来に向けての準備も進めていかなければなりません。
眞鍋は外航船メインでやってきましたが、洋上風力関係につながる作業船や石油や天然ガスなどのオフショアの分野も含めるとマーケットは倍以上あります。ウインチとクレーンを単体で捉えて目線を変えると、陸の産業もあります。船舶に縛られず、ウインチとクレーンをとことん極めていくのも、一つの道だと思っています。
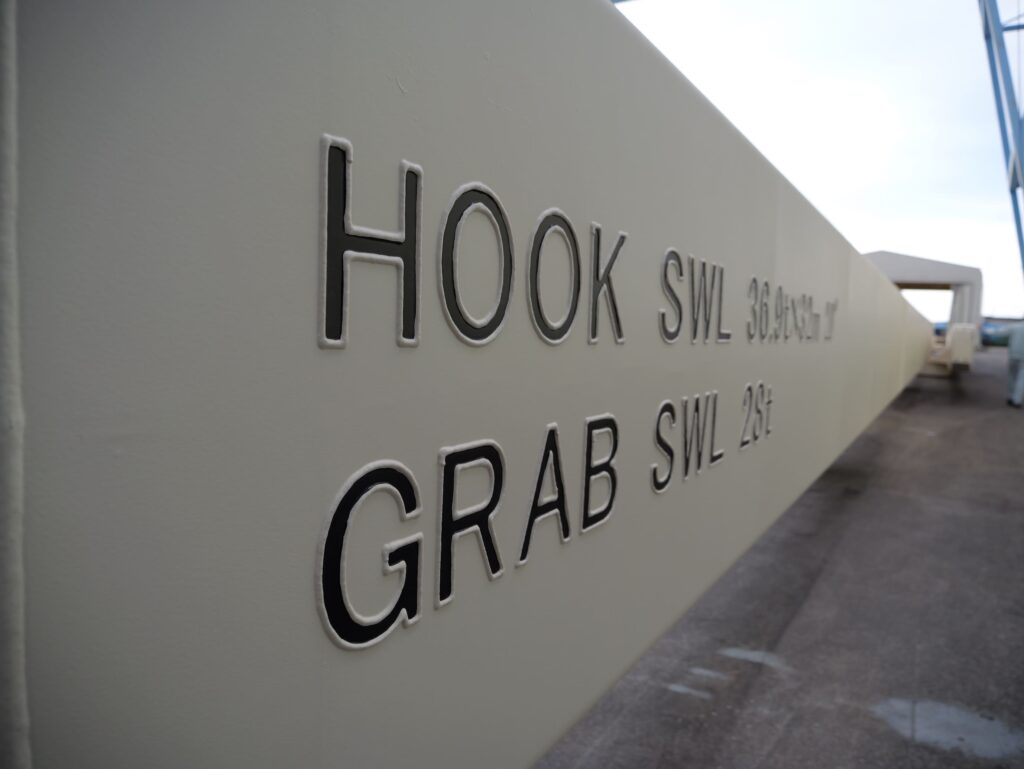
(第2話:「100年に一度の変化」に続く)
火花立ち上がる
眞鍋造機株式会社様
取材ご協力
眞鍋将之 社長
眞鍋哲夫 工場長
秦彰吾 様
取材
東海バネ工業 ばね探訪編集部(文/EP 松井 写真/EP 小川 )